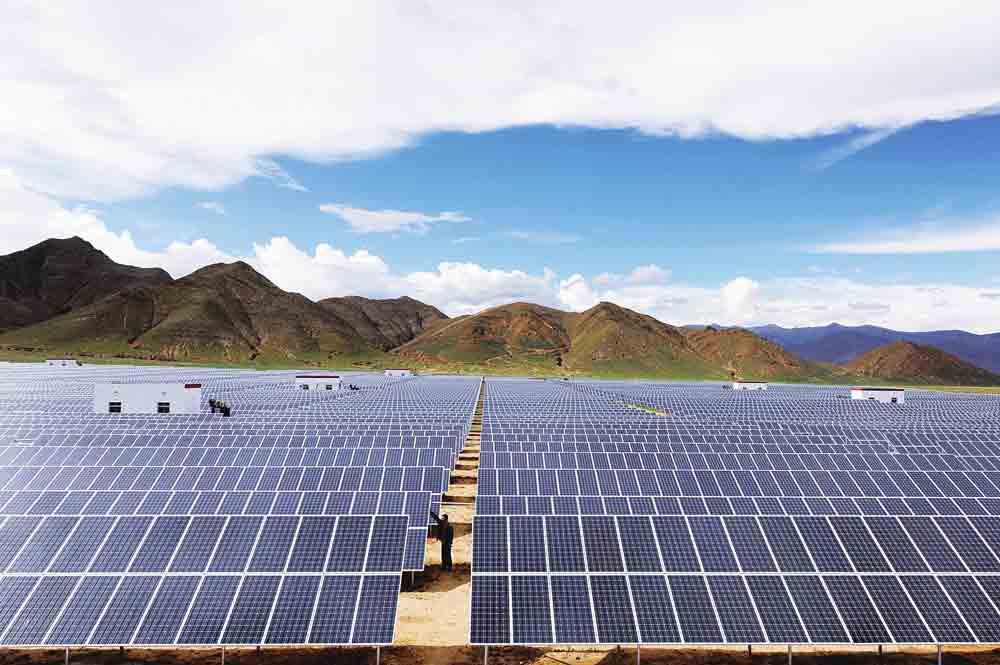
How To Build A Solar Power Station Ⅳ
6. Step-up transformer design and selection
Large and medium-sized grid-connected photovoltaic power stations basically choose 2*500kW centralized inverters, of which the transformer designed for supporting design is a 1000kVA low-voltage double-split transformer. It mainly adopts box-type substations with the characteristics of outdoor type, small size, easy installation and less maintenance, and the commonly used box transformers are American oil change and European dry change. American oil transformer has compact structure, small size, relatively low cost, strong overload capacity and easy installation. The main disadvantage is that the transformer body, load switch, etc. are enclosed in the mailbox, which is inconvenient to replace when a fault occurs, easy to seep and leak oil, and an accident oil pool needs to be built. There is a quality problem between the fuse and the internal structure of the tank, and there is no three-phase jumping device after the fuse is blown out, resulting in phase loss operation. The oil-changed heavy gas tripping can only jump the low-voltage side of the circuit, and the high-voltage incoming power supply cannot be cut; The European dry change space is relatively large, which is more convenient to install and easy to maintain. High and low voltage, transformer room independent partition, high operating safety factor. High and low pressure can be configured according to the user’s different cabinet types. The main disadvantages are large footprint, relatively high cost, general overload capacity, insulation supports, tap changer positions in the humid environment is easy to form flashing, creepage, such as untimely treatment may cause fault expansion.
Generally, a transformer comprehensive protection device is installed inside the box transformer, and there should be a variety of communication interfaces for data acquisition and sending to the control room.
7. Selection of high-voltage switches
At present, the photovoltaic power station mainly adopts metal armored central switchgear, circuit breaker configuration relay protection, standard complete sets of equipment technology is mature, mainly considering the brand and cost to make a comprehensive selection. The integrated protection device should have multiple communication interfaces for data acquisition and transmission to the control room.
The step-up transformer is generally arranged close to the centralized inverter and designed on a base platform.
8. Lightning protection grounding engineering
Galvanized flat steel is preferred for grounding materials for photovoltaic power plants. The average annual corrosion rate of hot-dip galvanized flat steel is 0.1mm/year, the steel has pitting corrosion, the rate of pitting corrosion is several times higher than the annual average corrosion rate, and the actual life is about 15~20 years. However, when the construction site is a strong corrosion area, steel copper plating materials need to be selected. Steel does not have pitting corrosion, belongs to slow uniform corrosion, copper corrosion rate in the soil is about 1/5 of steel, copper annual corrosion rate is 0.02mm/year, the life of pure copper grounding device can reach 50 years, the actual life of steel copper plated grounding device can reach 25~30 years.
Due to the large area of photovoltaic power plants, photovoltaic areas are generally not equipped with lightning rods. It is mainly connected to the grounding grid of the field area through the component bracket as grounding protection, and the investment proportion is relatively small. In the comprehensive utilization of photovoltaic power plants can not achieve fully enclosed management, grounding protection protection can not be sloppy. A good grounding grid is an important guarantee for equipment and personal safety.
9. Integrated automation system
Photovoltaic power plants should be designed according to the principle of “unattended”. The switching station should be equipped with a central control room, and the monitoring, control and scheduling management of the photovoltaic power generation unit and the mechanical and electrical equipment of the switching station should be completed through the centralized monitoring system based on the computer monitoring system. The design of the integrated automation system should be safe to use, technologically advanced and economically reasonable. The structure, technical performance and indicators of the system should be compatible with the scale of the photovoltaic power station and its position in the power system and the current development level of the monitoring system.
At present, the photovoltaic power plant monitoring system can monitor each photovoltaic incoming branch through the monitoring device of the combiner box, but it cannot monitor every battery module.
The end