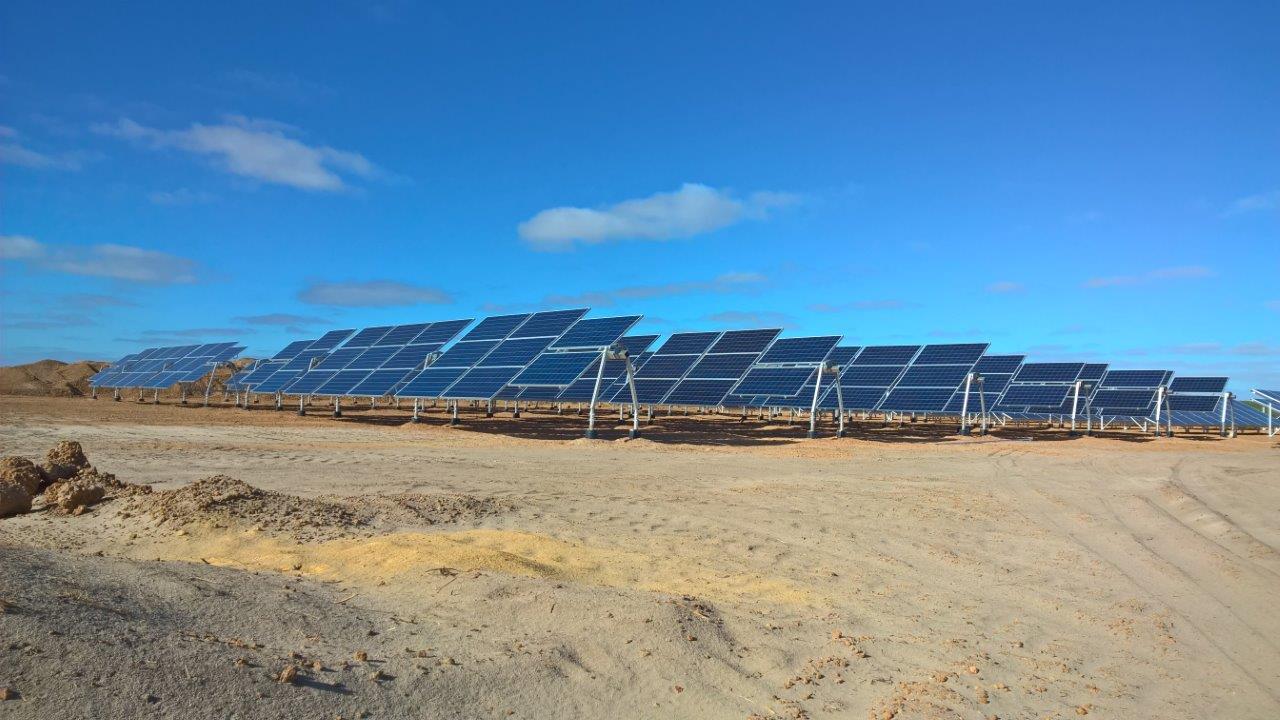
Wind Pressure Testing Is Essential For Solar Trackers
Responding to the test of climate conditions is becoming the new normal for solar developers and investors, requiring new measures to manage risks and ensure returns.
Understanding the importance of wind pressure testing and how different types of wind affect solar tracker design and production can help power generators secure the right single-axis tracker technology for their plants and regions.
A variety of factors affect how wind affects solar tracking bracket on each power station, from the local climate and topography, to the impact of other nearby structures or objects. Because no two PV plants are identical, each plant needs to be customized for a specific site, which adds to the complexity of designing these projects.
If the wind profile is not properly considered in the tracker’s design, asset owners can face a range of events, including remediation costs and downtime and lower power output, and ultimately miss financial targets.
Discern the technical nuances involved in designing for different types of wind and understand how proper tracker testing affects tracker design features, such as mounting angles and damping, to drive stable aerodynamics for long-term performance.
About the type of wind
Carefully assessing the wind conditions at the site can ask the right questions right from the start.
Changes in wind speed, turbulence, and direction can all have unexpected effects on solar trackers and their surroundings. Understanding the impact of wind helps developers and EPCs address uncertainties and optimize earnings.
Wind effects can be divided into three main categories: static, dynamic and aeroelastic.
Static wind forces apply stable and constant pressure to the tracker, which can cause the structure to deflect or bend, affecting the performance and accuracy of the tracking mechanism.
Dynamic wind forces are difficult to predict and their speed and direction fluctuate, which can cause significant vibration and pressure in the tracker, which reduces tracking accuracy and leads to misalignment of PV modules and wear and tearing of modules. These dynamic wind loads should be explained using advanced aerodynamic models that account for turbulence, gusts, and other variations.
When the tracker interacts with the surrounding air flow, aeroelastic wind forces are created. Aeroelastic effects include resonance, torsional flutter, and torsional dance, all of which can lead to uncontrolled vibration or oscillation that can lead to misalignment, reduced tracking accuracy, or component failure. Tracker design must focus on counteracting these effects for aerodynamic stability.
Tracker design must focus on counteracting these effects for aerodynamic stability. Each component in the tracker structure must be evaluated to ensure optimal wind load resistance. There are many potential failures to consider, including:
Resonance, which occurs when the frequency of gusts of wind matches the natural frequency of the structure, can lead to catastrophic failure.
Torsional flutter, a self-excited aerodynamic instability that can cause large vibration ups and downs in the torsional motion of the array, resulting in tracker failure.
Twist dance, which uniquely includes vertical movement. When the high wind speed exceeds the resistance of the structure, the tracker fails.
Understanding the effects of wind is not only critical to device design, but knowing how to deal with gusts can also optimize tracker performance. For example, knowing abnormal winds in specific parts of a PV site means that windproof fences can be used to reduce wind speed and turbulence, thereby improving the stability and accuracy of trackers. Complex sensors can be deployed to detect changes in wind and adjust the position of trackers to optimize power output. It is also possible to reduce the shape of the tracker, increase its stiffness, or design with specific materials that resist wind loads and aeroelastic effects.
Wind tunnel testing plays a vital role in the development of solar trackers. Small scaler models are used to evaluate how the new tracker handles any number of wind conditions, revealing design limitations early in development. After adjusting the design, a full-scale, cost-effective tracker can be produced to minimize risk.
Headwind terrain simulation is one of the key components of wind tunnel testing. This type of simulation replicates real-world obstacles that can affect wind, such as trees and buildings, and even other tracker arrays at the site.
Headwind behavior simulations include different elevation curves, modifiable surface roughness, movable barriers, and activity of various types of wind, including phenomena such as hurricanes and tornadoes.
Tailwind is achieved by retracting the angle. When designing wind-resistant solar trackers, careful consideration must be given to the retraction angle and associated static and dynamic wind loads. A useful mitigation strategy is damping, which dissipates or controls the vibrational energy or oscillations in the system.
Dampers are a key part of developing an optimal retraction strategy, especially for solar trackers with 0° retraction, they are susceptible to torsional forces that can lead to torsional and rotary movements along the torque tube shaft. During the development of the wind-resistant 1P tracker, different tilt angles were tested in the wind tunnel to develop the best retraction strategy. Tests have shown that a lower tilt angle provides less static load to the structure and less force on the overall system. The 0° inclination angle provides the lowest coefficient value because the lateral load is close to zero.
Higher tilt angles put additional stress on the structure, requiring more foundation or increasing foundation and torque tube size to withstand additional lateral forces. In contrast, it was found that a 0° retraction strategy with an appropriate degree of overdamping and stiffness to resist deformation required less foundation.
The ideal design for 0° collapse should balance stiffness, damping, and weight to control tracker costs, protect assets, and maintain efficiency. While it may be safe to store at a high inclination angle, it can increase wind loads on the foundation and other parts of the structure, requiring more robust systems or over-damping designs to mitigate dynamic fluctuations that cause aerodynamic instability.
Proper damping – suppression of vibrations and oscillations – is essential to ensure the stability of a solar tracking system. Determining the appropriate amount and type of damping depends on a variety of factors, such as the design retracting angle, beam length, and the quality of the structure.
Again, testing is key here. Systems with under-damping become unstable and require expensive mitigations, such as auxiliary dampers to address torsional forces that can cause tracker damage or even failure.
Since quality inspection is critical to determining the right configuration, it’s important to choose an experienced solar tracker solution provider with damper expertise that can meet project specifications, budgets, and schedules.